Markt: Ein Rad von der Stange hat jeder. Custom ist cool! Drössiger bietet die Möglichkeit beim eigenen Velo mitzureden und sich Ausstattung, Farbe und Design auszusuchen. Wir haben im Teil #1 gezeigt wie Alex von den Ganghelden in Nürnberg einem Kunden bei der Zusammenstellung seines Traumrads hilft. Jetzt, in Teil #2 wollen wir zeigen wie das bestellte Bike gebaut wird.
Im Ersten Schritt waren wir bei den Ganghelden in Nürnberg-Stein. Das ist der coole Radladen von Alex Ederer. Wir haben erlebt, wie gute Beratung durch einen erfahrenen Fachmann hilft Klarheit darüber zu gewinnen, wie das Rad sein sollte, dass den Besitzer glücklich machen kann. Hier noch Mal zum nachlesen:
Drössiger – so entsteht dein individuelles Wunschrad – Teil #1
Als erstes: Kopfarbeit
Das Rad wurde beim Termin im Rad-Shop konfiguriert. Der Händler checkt noch mal ob auch nichts vergessen wurde und übermittelt den Auftrag an den Innendienst bei JBS GmbH & Co. KG in Eschweiler. Damit die vielen Varianten, in denen jedes Rad angeboten wird schnell gebaut werden können, ist eine ausgeklügelte Logistik nötig. Warenwirtschaft und Köpfe müssen auf Zack sein, damit der Workflow nicht ins stocken gerät.
Als Zweites: Vorarbeit
In den Regalen liegen viele Rahmen, un-lackiert natürlich. Da sich jeder Kunde eine individuelle Farbe, auch die der Dekore aussuchen darf, startet der Aufbau mit einem rohen, nackten Rahmen. Ralf und seine Kollegen sind die Herrscher über Unmengen an Regalen, Kartons und Paletten. Auf über 5.000 Quadratmetern erstreckt sich ein Paradies für Fahrrad-verliebte. Er sucht alle Teile entsprechend des Auftrags zusammen und gibt alles an die Beschichtung weiter.
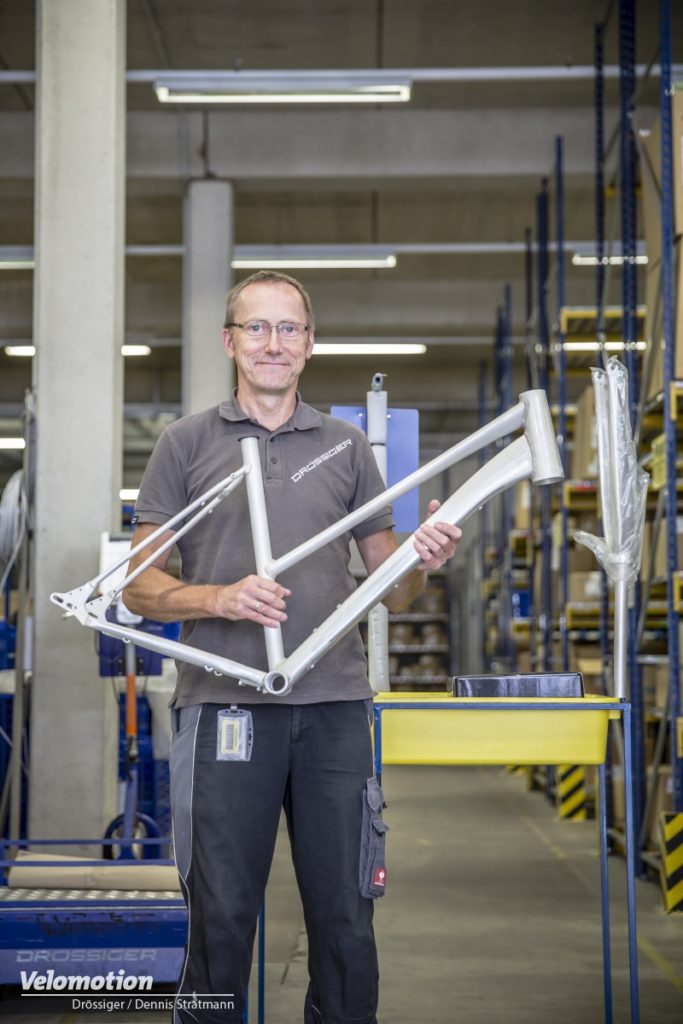
Dann kommt: Detailarbeit
Der Rahmen geht in die Lackierung, eigentlich müsste man sagen in die Pulverbeschichtung. Dort wird der Rahmen nochmal gereinigt und alle Stellen auf die keine Farbe soll werden abgeklebt. Der Rahmen erhält eine Elektrische Ladung die dafür sorgt, dass aufgesprühtes Farbgranulat daran haftet. Finki macht das schon ein paar Jahre und so wird die Beschichtung schön gleichmäßig.
Ist der Rahmen flächig mit Farbe bedeckt, wandert er in den Ofen. Unter hoher Temperatur verschmelzen die farbigen Kunststoffkügelchen zu einer festen Ummantelung. Das sorgt bei diesem Verfahren für eine besonders haltbare und unempfindliche Oberfläche.
Wenn der Rahmen aus dem Ofen kommt übernimmt Chico. Er druckt für jeden Kunden das persönliche Wunschdekor aus, ein wichtiger Schritt auf dem weg zum Traumrad. Dazu gehört absolute Präzision und Erfahrung. Die Menge an Farben, Kombinationen und Modellvarianten bietet einige Fettnäpfchen in die Chico treten könnte.
Bei jeder Rahmengröße muss er die exakten Bezugspunkte kennen um die Aufkleber perfekt positionieren zu können. Eine ruhige Hand und viel Übung sorgt für knitterfreies Anbringen. Die Decals sitzen auf einer Trägerfolie. Mit der werden sie aufgesetzt und angedrückt, dann wird die Trägerfolie entfernt. Nun ist das Chassis bereit für den letzten Gestaltungsvorgang, vor der Montage.
Die Folie, die zum Einsatz kommt, ist keine beliebige. Denn der Rahmen erhält noch das Finish in matt oder glänzend aufgetragen, wieder als Pulver-schicht und kommt ein zweites Mal in den Ofen. Diese doppelte Pulverbeschichtung sieht nicht nur hochwertig aus, sie macht den Rahmen auch noch widerstandsfähiger. Es wird bewusst auf den Einsatz von Nasslack verzichtet, da dieser mit hochgiftigen Lösungsmitteln verarbeitet wird und somit extrem schädlich für Mensch und Umwelt ist. Das gefällt uns!
Zu guter Letzt: Handarbeit
Der Rahmen sieht schon mal so aus, wie der Kunde sich das gewünscht hat. Zum Gesamtkunstwerk fehlt nur noch die Montage der Komponenten. Jetzt erst werden die Lagersitze und Gewinde auf das Finale Maß gefräst. So kann man sicherstellen, das alles perfekt passt. Tretlager, Ausfallenden und Steuerohr müssen exakt im richtigen Winkel zueinander stehen. Metall arbeitet bei Wärmeeinwirkung, beim Schweißen zum Beispiel und anschließend müssen die Rahmen wieder „gerichtet“ werden.
So nennt man den Vorgang bei dem man mit Hilfe von einem stabilen Tisch und Schablonen aus Metall die Maßhaltigkeit prüft und korrigiert. In den ersten Wochen nach dem Schweißen, bei der Lagerung, arbeitet die Kristallgitterstruktur des Materials noch nach. Durch das Finale bearbeiten der Montagepunkte zum spät möglichsten Zeitpunkt ist die Passung die bestmöglichste.
Die Laufräder für die Drössiger Bikes bauen sie selbst. Das entspricht der „No-Bullshit“ Politik der Marke. Schließlich soll das Traumrad nicht nur durch eine Traum-Optik bestechen, sondern auch durch Traum-Performance und hervorragende Haltbarkeit. Sven ist vom Fach und baut mit seinen Kollegen jedes Bike mit großer Fachkenntnis zusammen.
Das hier nicht im Fließband-Stil montiert wird trägt zusätzlich bei, optimale Qualität abzuliefern. So baut jedes Rad ein Mechaniker von A bis Z zusammen. Er kennt jedes Detail und fühlt sich für das Gesamtprodukt verantwortlich. Bei klassischer Fließbandmontage montiert jeder Arbeiter immer die selbe Komponente. Das geht schneller, macht es billiger und dadurch könnten einfachere Monteure eingesetzt werden. Die fahrfertigen Räder werden teilweise wieder zerlegt um sie für den Versand sicher zu verpacken. Natürlich gehen auch sämtliche Bedienungsanleitungen mit auf die Reise.
Sollten fragen auftauchen, so kann sich der Kunde immer an seinen Händler vor Ort wenden und der an die Drössiger-Crew. Das ist ein großer Vorteil! Das Rad ist kein anonymes Produkt, aus einer Massenfertigung. Der Ansprechpartner der das Rad mit dem Besitzer erdacht hat ist greifbar und ansprechbar, wenn doch noch etwas geändert werden muss. Selbst der Mechaniker, der die Teile zu einem Bike zusammengefügt hat ist nicht nur eine Nummer.
Im letzten Teil, Drössiger – so entsteht dein individuelles Wunschrad – Teil #3, haben wir wie das fertige Rad im Fahrtest.